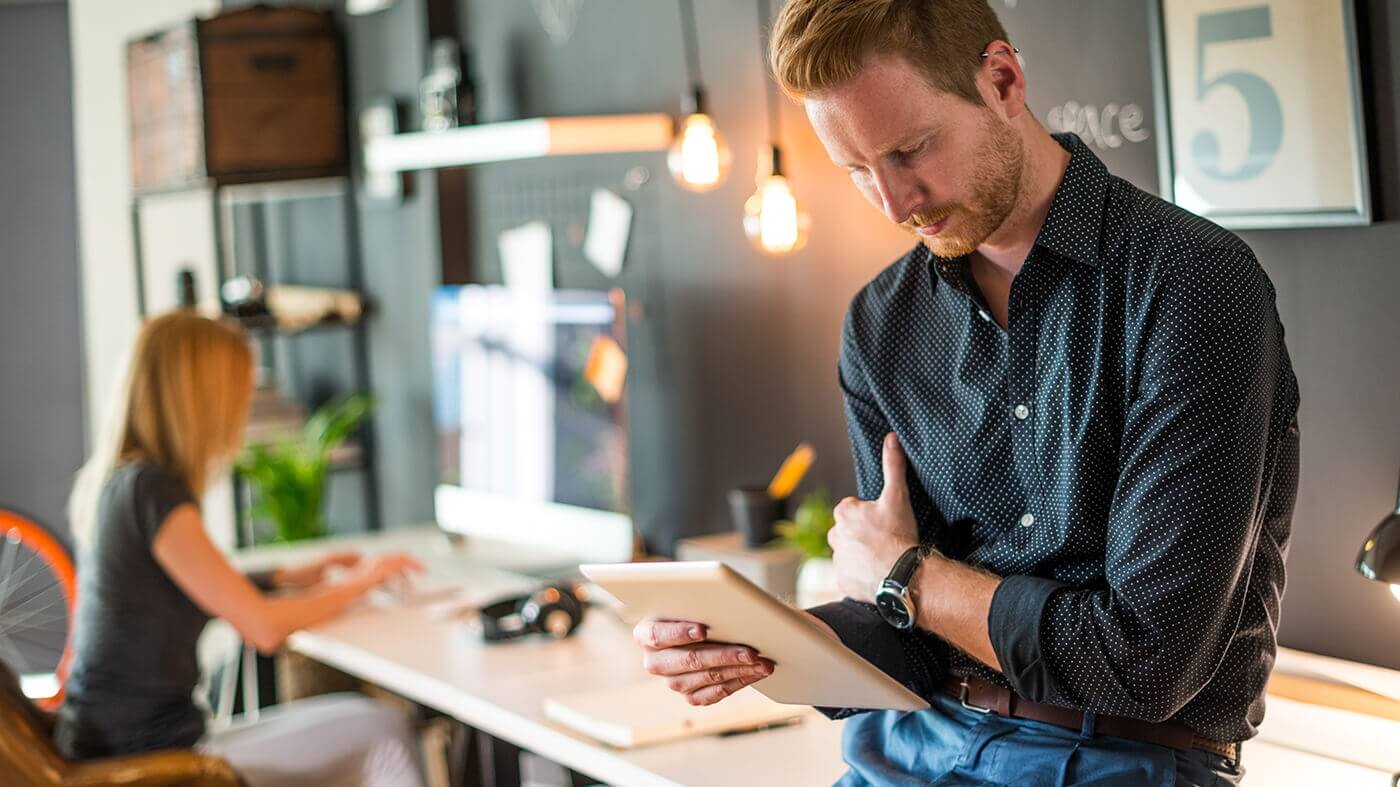
Reduce the food waste within your company with Dynamics Food
Reading time: 2 - 3 minutes
In early 2016, The Grocer launched their largest ever editorial campaign ‘Waste Not Want Not’ after food resource experts Wrap revealed that over 1.9 million tonnes of food were being discarded in the Food & Drink industry.
The worst part being that over 525 million edible meals were going to complete waste and they weren’t even being redistributed to those who needed it most. All of this with a backdrop of austerity, with more and more charities struggling to make ends meet.
Two years later, The Grocer reported that Tesco failed to hit their two-year target of eliminating food waste from their UK operation by the end of 2017/18. Instead, they saw food waste across the operation increase by more than 6,000 tonnes in a year.
Since the launch of ‘Waste Not Want Not’ over 60 retailers and suppliers have committed to doubling their redistribution efforts by 2020 – the equivalent of saving 30,000 tonnes in five years. Clearly, the retailers are making a conscious effort to tackle the food waste conundrum, but it remains abundantly clear they will never eradicate the issue completely.
Ensure you don’t over-order or let faulty products escape your warehouse
To help reduce the amount of product that goes to waste, Dynamics Food will give you the ability to manage and improve your production’s entire quality process by capturing test results, creating rework orders and regulating stock to ensure faulty or below specification products don’t make it out of your warehouse.
Another common mistake which creates waste is buying in bulk as it slashes the bill for manufacturers. The incentive tends to lead procurement departments to over order ingredients to obtain a cheaper unit price. If the demand isn’t there, you’re left with a load of out-of-date wasted stock.
A lot of manufacturers measure their ingredient costs by backflushing – where volumes and prices are only added up at the end of production and they don’t include deductions for any wasted stock created by production difficulties. This means that next time an order is placed the quantities are a lot higher than they need to be, which in turn creates excess waste.
Dynamics Food provides real-time visibility of stock availability and movements (with sell-by dates, shelf life and catchweight all considered) to enable your team and users to make reliable decisions in the knowledge of exactly the quantity of what you need to order and deliver.
Why do Food manufacturers choose Technology Management?
Technology Management helps manufacturing, and distribution business transform their processes and operations with Microsoft Dynamics. Dynamics Food is our offer of Microsoft Dynamics 365 Business Central/Dynamics 365 to provide a complete end-to-end ERP software for food companies. To learn more about how Dynamics Food can help you reduce waste, please visit: Dynamics Food
Some of the companies using Dynamics Food include well-known names as Bounce Foods, Copernus, County Confectionery, David Berryman, Faccenda Foods, Forza Foods, Gressingham Foods, Kent Foods, Laila's Fine Foods, Nantwich Cheese Company, Neal's Yard Dairy, Pipers Crisps, Rondanini and Zeina Foods.