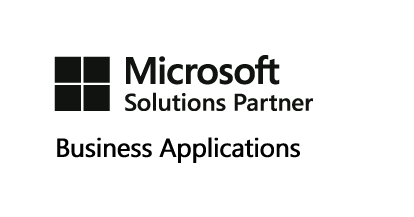
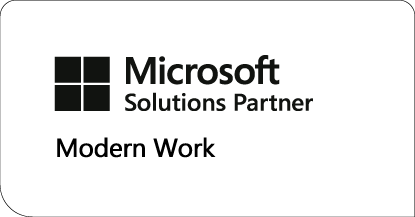

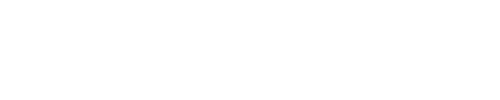
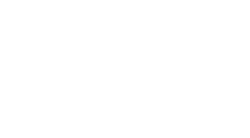
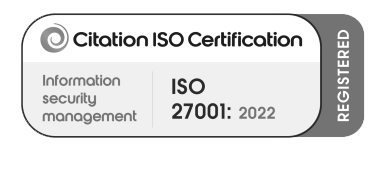
In food warehouses, it’s essential to move quickly, or things can start to go bad… literally. Challenges like Zoning and Cross-docking (that we covered in part 1 of this blog series) added to the need for farm-to-fork traceability and close management of shelf lives only adds to the already demanding requirements of warehousing and distribution in today’s food industry.
Full traceability is key from a food safety perspective. In the event of a recall, companies need to be able to quickly locate what products are contaminated and where they were sent. Then you also need to quickly identify the various ingredients to determine how/where the contamination occurred – and stop it in its tracks.
We recognise you often have to deal with various different quality systems, including when and how products leave the warehouse, often through third party logistics (3PL) companies. If this process isn’t integrated with your business systems, checks can be missed and traceability for items once they leave the warehouse becomes an uphill battle and in event of an emergency it causes additional, unnecessary downtime and panic.
Food manufacturers produce in high volume and have rapid inventory turnover, making it virtually impossible to track information by paper. Traditionally, businesses have kept paper invoices and shipping documents that could take days or weeks to sort through during a recall. However, in today’s just-in-time supply chain, a company is expected to take action within hours when food safety is at stake.
With a food industry ERP system in place, information about raw ingredients and finished products is collected into a single database. In the event of a recall you will be able to react more effectively and keep any damage to a minimum.
Simply put, manual data entry from paper usually results in error rates that are too high for reliable traceability. Automated data collection tools are designed to help employees quickly capture the data needed. They walk employees through each step of the process for in-house materials transfers, intra-plant transfers, putting away finished products, picking products for shipment and creating shipments.
Using wireless and mobile devices/barcode scanning devices in the warehouse, also means information about lot numbers is captured in seconds and transferred automatically to your core ERP solution.
In an industry plagued with product recalls, a food production firm needs to be able to demonstrate that it can track its product and the ingredients therein both upstream and downstream - from raw ingredients to the finished goods and vice versa. To do this, data from every point in the supply chain must be recorded to provide an audit trail. This is why many food and beverage firms choose to implement specialist ERP system, like Dynamics Food, to provide a centralised system to manage all this data.
In the supply of perishable food products, large losses can be incurred between farm and fork if shelf life is not correctly tracked.
Further complications are added with different retailers accepting different minimum number of days remaining until the “display by” or “use by” date.
Huge value can be added by optimising your warehouse management, by taking into account the remaining shelf life of a product, and matching it to the requirements of the subsequent part of the handling chain.
With system-directed picks/put-aways from ERP, supported with integrated handheld devices, you can ensure the products with the earliest used-by dates are selected for dispatch to the right retailers to prevent spoiled stock. The routing for multiple picks can also be optimised – saving time and reducing wear and tear on your equipment and your teams!
And it’s not just about how much space you have in the warehouse that can make shelf-life difficult to manage; it's about optimising the space to avoid unnecessary labour. Keeping fast-moving and short use-by inventory near the front of the facility so truck-lift drivers aren't constantly traveling to the farthest reaches of the warehouse is just one solution that can help radically optimise the warehouse.
Information is power, so having a ERP/business software solution specifically developed for the needs of food processors and distributors is fundamental to maximising warehouse efficiency, minimising stock and boosting order and shipment accuracy.
Having ERP in place will help you manage every step of the manufacturing and supply process: from order processing to ingredients/goods in through to final delivery to store/RDC (regional delivery centre).
Much like consumers who purchase food several times a week to provision themselves for meals that they eat several times a day, food and beverage manufacturers must maintain and turn over their inventory more quickly and frequently than other warehouses.
Be prepared to fulfil demands quickly and easily from the start of your manufacturing process right through to goods out with integrated ERP for the food industry such as Dynamics Food.
Attend our complimentary briefing: Boost performance with a single business software solution with Dynamics Food on either Tuesday 20th March from 10:00am-12:30pm in Wolverhampton, or alternatively Wednesday 9th May from 10:00am-12:30pm at Microsoft London.